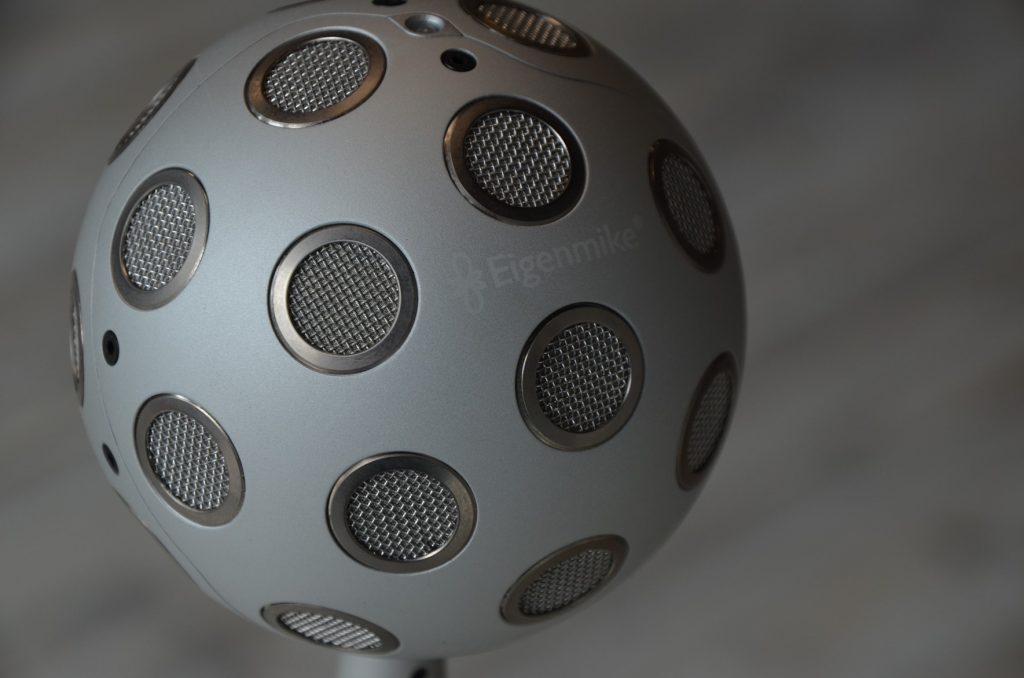
April 23, 2024
When you’re sitting on a park bench, you probably never wonder what it’s made of. Maybe it’s because you think it’s just wood – and you haven’t the faintest idea that it’s a so-called wood-plastic composite. In industry as well as in everyday life, the share of composite products is increasingly growing, and in the future – due to the high demand for composite materials in such strong industries as automotive and military – further prosperity for them is predicted.
Composites are also an important area of research at the InnoRenew CoE research institute; one of the research groups is named Renewable Materials Composites, after all. Three researchers from this group are exploring ways to further improve the properties of wood-plastic composites. But the beginning of this story goes back to the United States, to the time before InnoRenew CoE was founded.
In 2012, the NEWBio (The Northeast Woody / Warm-season Biomass Consortium) project was launched in the USA to explore use of lignocellulosic biomass for bioenergy and bioproducts. The project involved work in transportation fuels, biochemicals, bioproducts and education, focusing on woody and perennial crops (short rotation willow, switchgrass and miscanthus) and technologies to turn these materials into products.
During the NEWBio project, in a wide area of the northeastern United States (Pennsylvania, New York, Ohio, New Jersey and West Virginia), researchers planted demonstration sites by feedstock that were subsequently used for experiments. They chose marginal farmland and reclaimed mine land that was not intended for agricultural activity.
The project, worth about ten million dollars, came to an end in 2018. But one of the directions of the research was continued within the InnoRenew project in Slovenia, led by Dr David B. DeVallance.
In the NEWBio project, Dr DeVallance participated by leading bioenergy and bioproducts education performed at West Virginia University. In addition, he was part of a research group that, among other things, focused on evaluating the use of willow in wood-plastic composites.
“When I left West Virginia University, the research on wood-plastic composites from torrefied and non-torrefied short rotation shrub willow was in its infancy,” says Dr DeVallance. “We decided to further explore this research at InnoRenew CoE within the Renewable Materials Composite Group. Specifically, we wanted to determine the mechanical, thermal and water resistance properties of wood plastic composites made from mixtures of willow, torrefied and non-torrefied, and polypropylene.”
Biocomposites generally refer to composites made from at least two or more materials that include at least one naturally occurring component. When combined with polymers, the naturally sourced materials (fibers, particles, etc.) generally act as reinforcements or fillers to produce composites that are more suitable for certain applications. Biocomposite use in various works and industries – especially in automotive, military and aerospace – is growing rapidly.
Wood-plastic composites are often used for outdoor decking and fences; increasingly, they are also used for other building elements as well as objects, such as park benches, flowerpots or summer kitchens, where the combination of plastic and wood brings the desired effects. Wood is not only added to plastic to improve its properties but also for its sustainability aspect as this reduces the consumption of plastic by thirty to fifty percent.
With current research, the Slovenian team of Dr DeVallance, Jaka Gašper Pečnik and Dr Matthew Schwarzkopf would like to improve the quality or usability of such biocomposites by adding torrefied wood. Torrefication is a thermal process of wood treatment, at temperature from 200 to 300 °C, in which wood reaches higher calorific values and becomes lighter, more brittle and more hydrophobic than non-torrefied wood. In the case of WPCs, there is potential to use these torrefied materials to improve the thermal and water resistant properties
Slovenian researchers in this study prepared samples from a short rotation shrub willow grown in Pennsylvania (USA), which was ground and torrefied at two different temperatures (225 and 300 °C) using a tube furnace. The material was then mixed with polypropylene in various ratios of wood to polymer. The wood-plastic composite was made with an extruder with a double rotary screw and moulded into small pellets. These pellets were then compressed into test specimens for testing mechanical and physical properties.
“The idea is that torrefied wood is more hydrophobic than non-treated wood and can potentially lead to better bonding and higher strength,” says Dr DeVallance. “Also, because torrefied wood is more hydrophobic, the resistance to moisture is improved.”
Although they are in the middle of research, some results have already been detected. The Slovenian researchers observed that bending strength and elasticity decreased with inclusion of torrefied willow, with the highest reduction found in the modulus of elasticity when using wood torrefied at the highest temperature (300 °C). In tensile tests, however, the results indicated that while tensile strength was reduced with the addition of torrefied willow, elastic properties slightly improved. In addition, composites made using wood torrefied at 300 °C resulted in higher water resistance (lower water absorption), which increased with higher loading levels of torrefied wood.
So far, researchers have performed tests with one variety of willow (Millbrook), torrefied at two different temperatures. They are currently preparing new samples for new tests that will contain the wood of two other varieties of willow (Fabius and Fish Creek). In addition to the mechanical, physical and absorption properties of the materials, they will also study the effect of regrinding the material in order to be able to evaluate the possibilities for recycling or re-use of such material.
Researchers hope that these preliminary studies, which are expected to be completed in August this year, will lead to new funding in Slovenia and Europe, which would enable the research to continue. The results could be extremely valuable for the economy, especially in construction (for wood-plastic decking), the automotive industry (for car panels) and for all companies that produce plastics (for fillers).