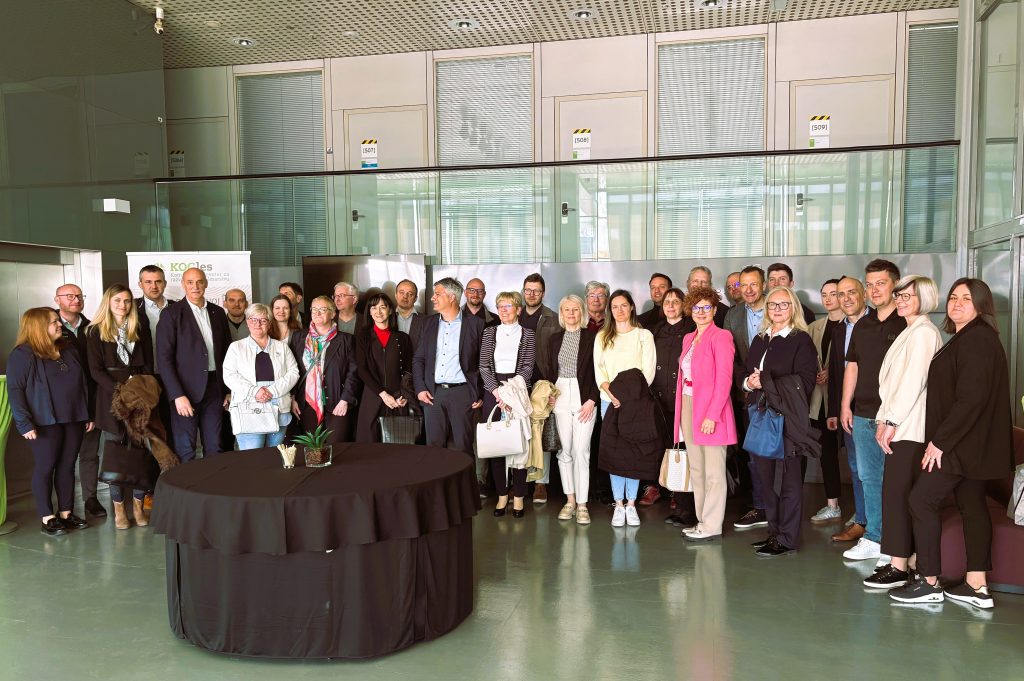
April 14, 2025
An essential aspect of sustainable building is the development of innovative eco-friendly materials, which is a focus of the Renewable Materials Composites (RMC) research group at InnoRenew CoE.
Dr. Laetitia Marrot, researcher in the RMC group, works on the valorization of biomass from annual plants (hemp and flax) for the development of sustainable composites. These annual plants can be used in many ways: as a precursor for bio-based carbon production (visit the FAÇADE project website to learn more about this topic), as an insulation material like hempcrete or as a fibrous material reinforcement, to cite just a few applications.
One of Dr. Marrot’s ongoing projects is exploring ways to reinforce concrete with textile fabrics made from flax. This study was initiated last year in collaboration with the textile and concrete departments (HOFZET and ZELUBA, respectively) of the Fraunhofer WKI.
Concrete has been one of the most important construction materials since the invention of Portland cement by Joseph Aspdin in the early 1800s in England. Today the global production of concrete exceeds 4.4 billion tons annually. As poorer countries rapidly urbanize, that number is expected to rise to over 5.5 billion tons by 2050 [1]. Concrete’s ongoing popularity for developing new modern infrastructure all over the globe is due to its high compressive strength, durability and low cost. However, all materials come with certain disadvantages when used for various applications, and concrete is no different.
The main drawbacks of concrete, when used in construction, are its brittleness and unreliable tensile strength. To resolve these issues, the construction industry has proposed different methods to reinforce concrete – steel bars being one of the most common. However, while steel provides an adequate reinforcement (mainly tensile), it is prone to corrosion if exposed to oxygen and water from the surrounding environment. An additional layer of concrete is then needed to cover the steel bar and protect it, leading to an unnecessarily heavy material, higher cost and energy that contributes to carbon dioxide emissions and increases the environmental impact.
In the 1970s [2],[3], science turned to more eco-friendly ways to reinforce concrete, and an idea emerged that would have steel bars replaced by textile materials. Textile reinforced concrete does not require an additional concrete protective layer since the material itself is not prone to corrosion, unlike steel. This results in a significant reduction of material usage and cost. Textiles made of metallic, ceramic, synthetic polymers, inorganic or natural fibers have been considered for this purpose. Natural fibers are available almost anywhere in the world and are plentiful. What makes them so attractive is that they are biodegradable and renewable while also displaying desirable mechanical performance. Flax fibers appear to be among the strongest plant fibers, having particularly high specific tensile properties that are comparable to those of glass fibers [4]. The thread system of a textile, also known as weave, is responsible for some material properties, such as ensuring sufficient dimensional stability and mechanical resistance.
Although flax fibers show great potential for reinforcement, without protection they can be affected by the concrete environment. Indeed, formation of the cementitious matrix results in a high alkaline environment that is tough for fibrous materials. Depending on their composition, fibrous materials resist differently when exposed to such conditions. For example, glass fibers showcase low corrosion resistance in a high alkaline environment, which leads to the development of a specific type of glass fiber for the reinforcement of concrete (AR-glass) to avoid its degradation. In natural fibers, dissolution of chemical components, such as hemicellulose and lignin, occurs in an alkaline environment [5]. This problem can be overcome either by modification or protection of the fiber surface; it can also be overcome by using a less aggressive composition for the cementitious matrix.
In Dr. Marrot’s project, the former option was used. Several bio-based coatings were examined to protect the fiber surface from the alkaline environment of the cementitious matrix, leaving the chemical components of the textile intact. Different textile contents (between one and six percent regarding the weight of concrete) were used for manufacturing composite samples in order to see the effect of textile reinforcement on the flexural properties of the composites. Holes were drilled in the textile to widen its opening and allow a mechanical anchoring between concrete and textile.
In future steps, two batches of textile reinforced concrete will be tested and compared. One batch will have its flax textile reinforcement protected with a bio-based coating, and the other batch will be reinforced by an uncoated flax textile. Hence, beneficial effect of each coating for textile protection, adhesion with cementitious matrix and mechanical performance will be assessed.
Results could be of great significance to civil engineering and the construction industry, illustrating textile reinforced concrete’s sustainable, structural and economic value.
Dr. Laetitia Marrot, Marie Skłodowska-Curie Action fellow,
Filip Majstorović, RMC group visiting researcher
The FAÇADE project has received funding from the European Union’s Horizon 2020 research and innovation programme under the Marie Skłodowska-Curie grant agreement No. 898179.
Bibliography
[1] J. Hilburg, “Concrete production produces eight percent of the world’s carbon dioxide emissions,” The Architect’s Newspaper, Jan. 02, 2019. https://www.archpaper.com/2019/01/concrete-production-eight-percent-co2-emissions/ (accessed Oct. 22, 2020).
[2] M. Curbach et al., “Sachstandbericht zum Einsatz von Textilien im Massivbau,” Kurzber. AUS Bauforsch., vol. 40, no. 1, 1999, Accessed: Oct. 22, 2020. [Online]. Available: https://trid.trb.org/view/963177.
[3] W. Brameshuber, Report 36: Textile Reinforced Concrete – State-of-the-Art Report of RILEM TC 201-TRC. RILEM Publications, 2006.
[4] A. Bourmaud, J. Beaugrand, D. U. Shah, V. Placet, and C. Baley, “Towards the design of high-performance plant fibre composites,” Prog. Mater. Sci., vol. 97, pp. 347–408, Aug. 2018, doi: 10.1016/j.pmatsci.2018.05.005.
[5] R. D. Tolêdo Filho, K. Scrivener, G. L. England, and K. Ghavami, “Durability of alkali-sensitive sisal and coconut fibres in cement mortar composites,” Cem. Concr. Compos., vol. 22, no. 2, pp. 127–143, Apr. 2000, doi: 10.1016/S0958-9465(99)00039-6.